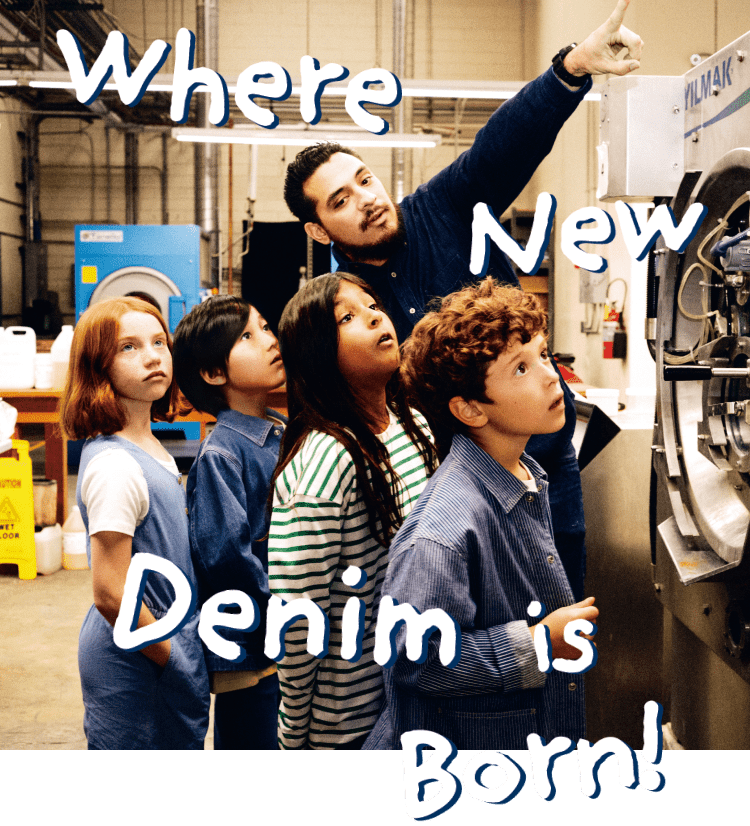
Sylvie, Issa, Surya, Elan
Jeans Kids Club
Welcome to the Jeans Innovation Center, where the denim of the future is born. This group of kids from LA, the next generation of doers, took a field trip to the lab.
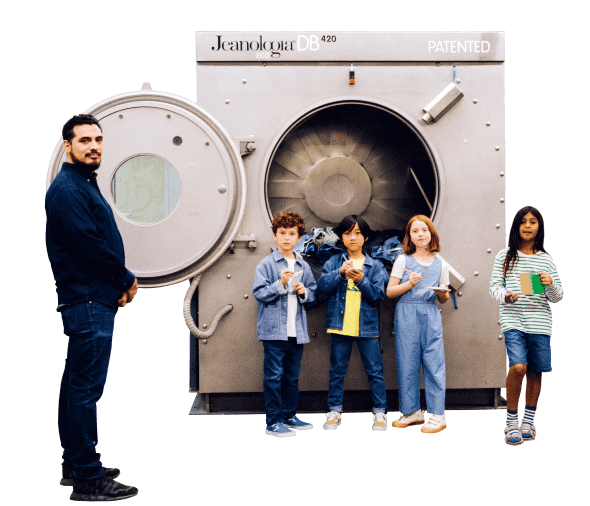
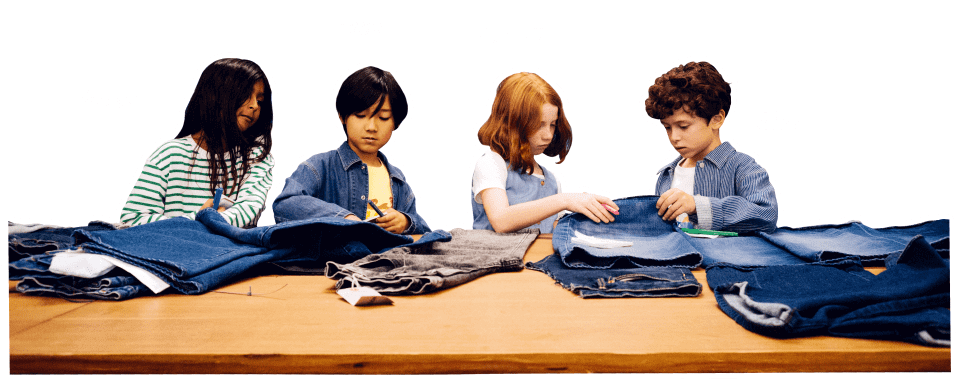
These kids got a kick out of the denim samples JIC keeps on-hand for research, in a variety of wear levels. Touching each one, they took lots of notes.
The Jeans Innovation Center, JIC for short, came to life in 2016. A facility for jeans research and development, this is the birthplace of UNIQLO denim, where it continues to evolve, and where future techniques for processing and production are conceived. A place where prototypes are fashioned daily, this lab allows for every step to be explored, from patterns and cutting to finishing washes. Thus far, the lab’s greatest achievement is something called “Blue Cycle” technology that cuts the water needed to distress jeans by as much as 99% (based on a comparison of our men’s regular fit jeans from 2017 and the updated item released in 2018. Varies by product). Recently, we had a visit from a group of local kids, dressed up in denim outfits. These four friends were astounded by the enormous washing machines in the middle of the center, each one almost as big as them. For starters, they spent a minute with Thomas, the nice man who cuts patterns in the sewing room. “Is this the part that turns into the pocket?” Issa asks him, full of curiosity. Feasting their eyes on the different patterns and the wall stuffed with sample fabrics, they soon headed over to the Blue Cycle area.
Cut & Sew
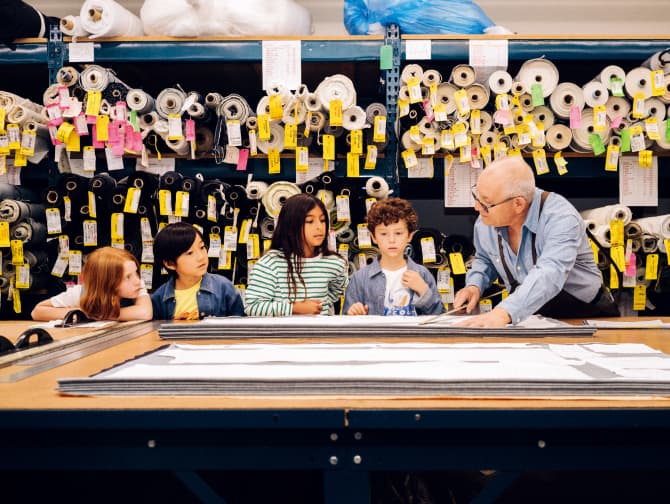
Starched denim cloth is piled ten sheets thick and marked up with a pattern, then cut to size using a specialized machine that works like a reciprocating saw. “There’s the pocket!” says Surya, in the striped shirt.
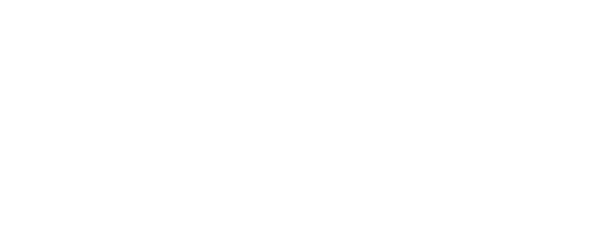
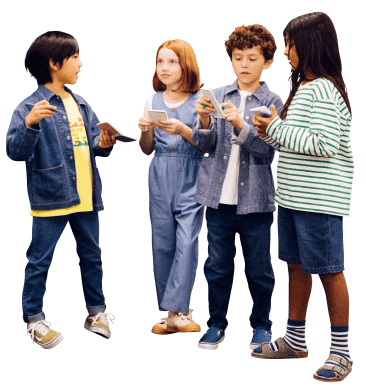
What makes the technology so unique is that it realistically mimics the effect of a laser beam. Carefully, the kids peer into a machine loaded with a pair of rigid jeans. Then suddenly, a puff of smoke... and then a flame and a big “BZZZ!” that makes Surya block his ears and hop into the air. In a matter of seconds, the denim looks well-worn and distressed. Elan reaches out and touches the torn area. “Did a laser do this?” “That’s right,” says Juan, the technician. “It burns the fabric in a pattern made on a computer. We’ve installed setups just like this one at our factories in places like Bangladesh.” It used to be jeans were distressed at factories by hand, using sandpaper. Different levels of expertise led to variable results, but more importantly, presented health risks to personnel dust from the torn fabric. Now that lasers have been introduced, the factories can mass-produce jeans of consistently high quality in a healthy manner.
Next up, the kids visited the washing machines up close to see another feature of Blue Cycle Jeans. Darwin, the engineering manager, opens the door. Strong mist comes spraying out, but there’s hardly any water inside. “What’s that mist doing?” asks Sylvie. Washing jeans involves a number of steps. First, the starch is released, turning what we call “raw denim” into washed fabric. After that, the jeans are washed repeatedly to give them a realistic faded look and the stress lines called “atari.” Doing so ordinarily requires huge amounts of water. What has revolutionized this process is a mist-washing technique called “nano bubble washing.” Instead of being dunked in water, the jeans are sprayed with small amounts of vapor at high pressure, in a high-efficiency wash. As a finishing touch, the fabric is distressed via “ozone washing.” This involves using ozone gas to oxidize the dye that’s in the denim, for a strong and natural bleached effect.
That said, small amounts of water are still used. Taking responsibility, JIC has also developed a specialized water recycling system. In the new process, the power of ozone and minerals is harnessed to remove the dyes and chemicals from the blue water left over after washing, so that the water can be filtered and restored to clarity.
The techniques of the future are helping us to create authentic-looking distressed jeans you’ll want to wear forever. Our hope is that these four kids will want to keep on wearing LifeWear jeans once they’ve grown into fine adults. This hope is what sustains our continued research at the JIC.
Laser Processing
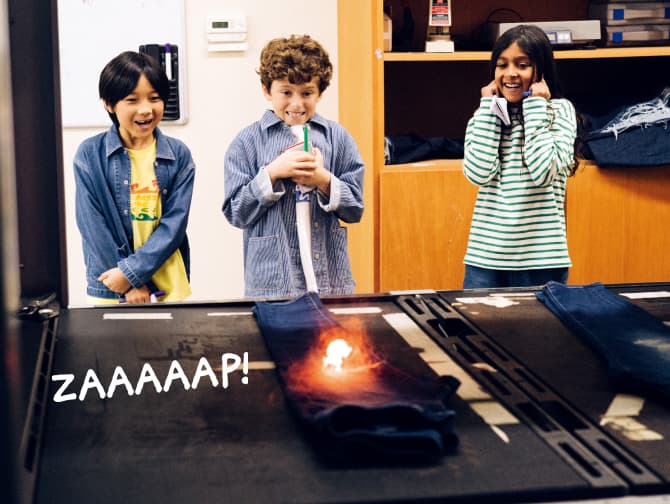
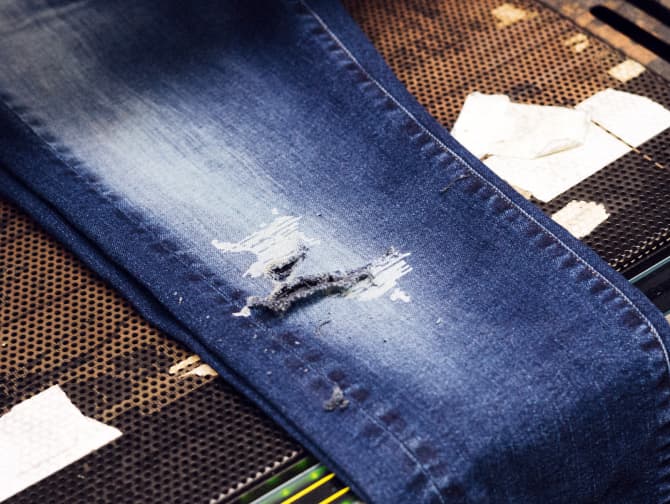
Intense processes like laser tearing release flames and sparks. It’s a clean process, since any scraps are incinerated on the spot, while the smoke is sucked downward.
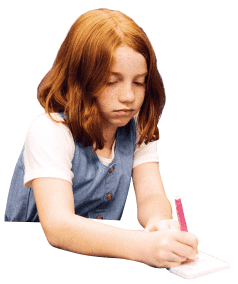
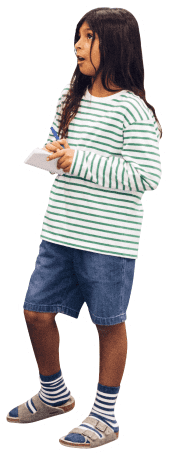
Next up, the kids visited the washing machines up close to see another feature of Blue Cycle Jeans. Darwin, the engineering manager, opens the door. Strong mist comes spraying out, but there’s hardly any water inside. “What’s that mist doing?” asks Sylvie. Washing jeans involves a number of steps. First, the starch is released, turning what we call “raw denim” into washed fabric. After that, the jeans are washed repeatedly to give them a realistic faded look and the stress lines called “atari.” Doing so ordinarily requires huge amounts of water. What has revolutionized this process is a mist-washing technique called “nano bubble washing.” Instead of being dunked in water, the jeans are sprayed with small amounts of vapor at high pressure, in a high-efficiency wash. As a finishing touch, the fabric is distressed via “ozone washing.” This involves using ozone gas to oxidize the dye that’s in the denim, for a strong and natural bleached effect.
Nano Bubble Washing
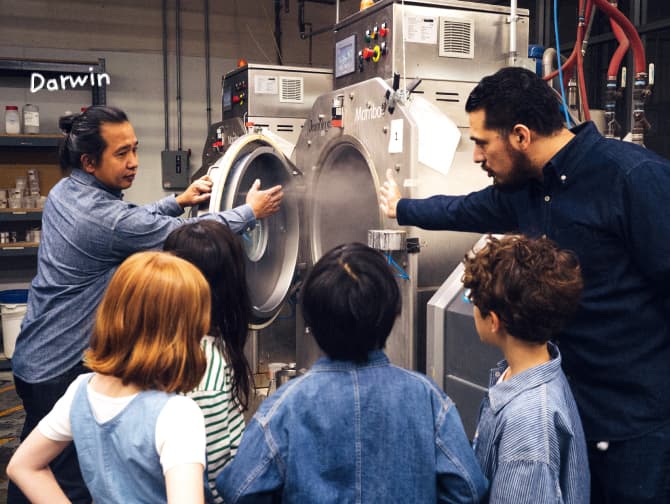
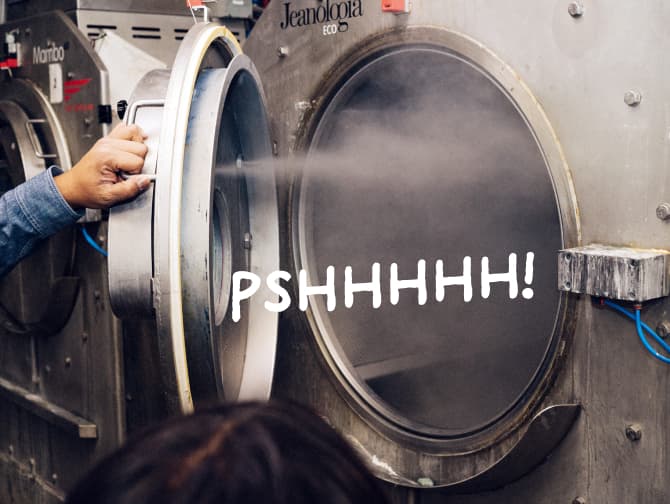
Check out the mist coming from this door. Ejected at high pressure, it pulls colour from the denim.
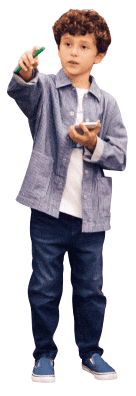
Ozone Washing
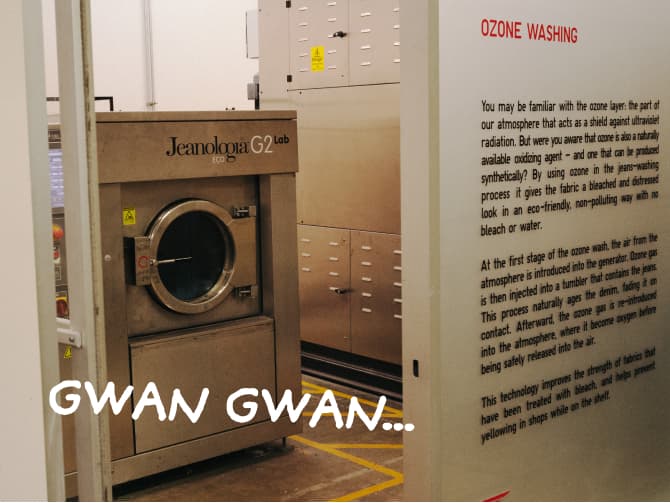
Ozone is used to bleach jeans in this tumble washer.
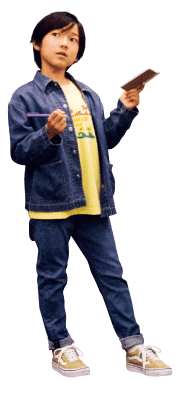
That said, small amounts of water are still used. Taking responsibility, JIC has also developed a specialized water recycling system. In the new process, the power of ozone and minerals is harnessed to remove the dyes and chemicals from the blue water left over after washing, so that the water can be filtered and restored to clarity.
The techniques of the future are helping us to create authentic-looking distressed jeans you’ll want to wear forever. Our hope is that these four kids will want to keep on wearing LifeWear jeans once they’ve grown into fine adults. This hope is what sustains our continued research at the JIC.
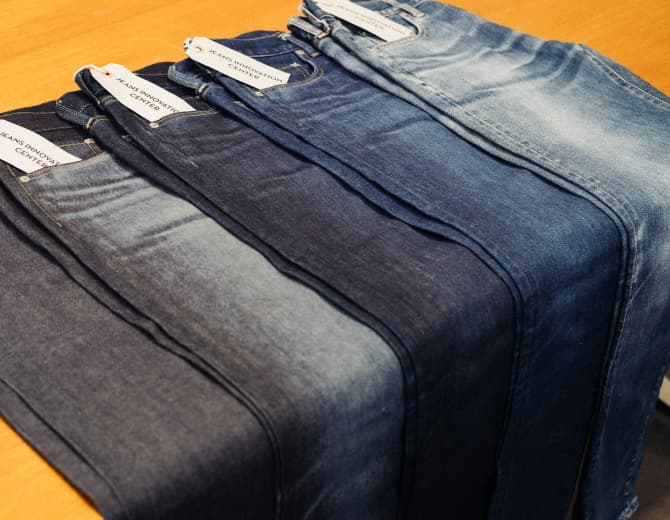
Sample pairs exemplify each step. From left to right: raw denim; a pair after laser processing only; two pairs after different nano bubble washes; and a pair processed using ozone washing.
- Elan
- Issa
- Sylvie
-
- Jumpsuit (This product is not available in Canada)
- Cotton Inner T-Shirt (This product is not available in Canada)
- Surya
-
- Striped Crew Neck T-Shirt (This product is not available in Canada)
- Kids Stretch Denim Easy Shorts $24.90
- Socks $14.90
- Photography by Kohei Kawashima
- Styling by Mitsuru Kurosawa
- Hair & Makeup by Anna Kato
- Coordination by Megumi Yamano
- Special thanks to Naoyasu Mera, Aya Mutoh
- Français
- English