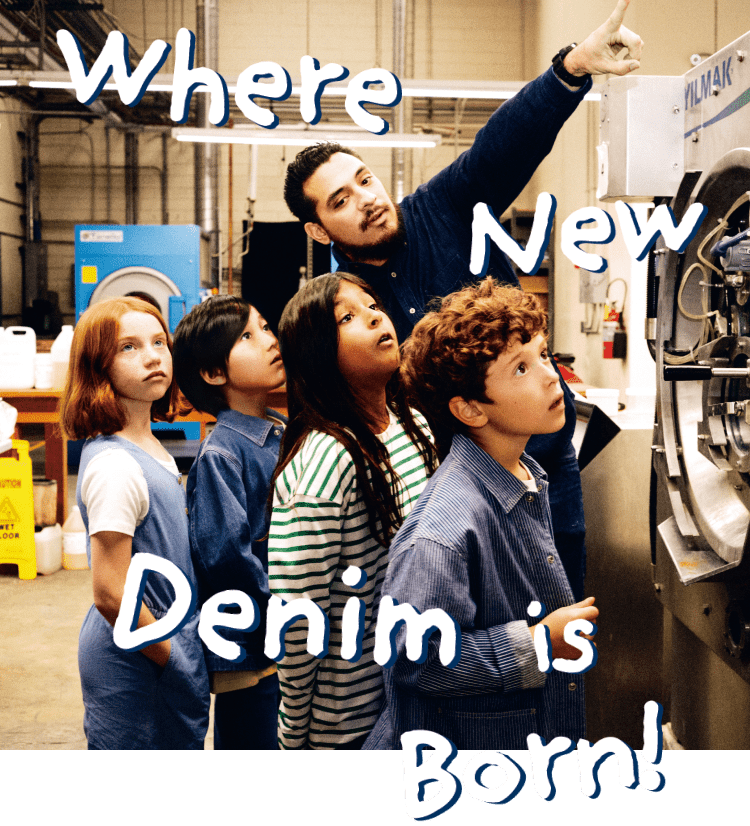
Sylvie, Issa, Surya, Elan
Nos écoliers, visiteurs d’un jour
Bienvenue au Centre d’innovation du jean, là où est fabriqué le denim de demain. Ce groupe d’écoliers de Los Angeles, qui sont les forces vives de la prochaine génération, ont fait une excursion dans notre laboratoire.
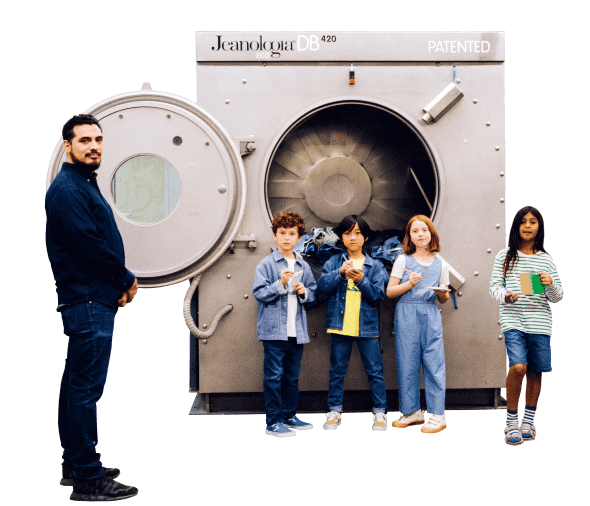
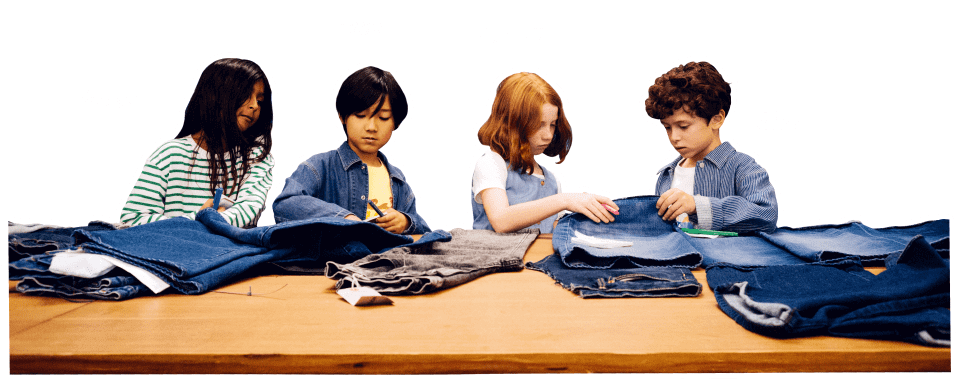
Durant leur excursion en immersion, nos visiteurs d’un jour se sont amusés avec des échantillons de denim que le laboratoire utilise pour ses recherches, et qui présentent des degrés d’usure différents. Nos écoliers n’ont pas manqué de prendre des notes en testant chacun de ces échantillons.
Le Centre d’innovation du jean (Jeans Innovation Center) a vu le jour en 2016. Cette installation, dédiée tout spécialement à la recherche et au développement de nos jeans, est le berceau du denim UNIQLO. C’est ici que ce matériau fétiche de la marque continue d’évoluer au fil du temps, et où sont mises au point nos futures techniques de traitement et de fabrication. C’est dans ce laboratoire aussi que de nouveaux prototypes sont façonnés chaque jour. À l’instar de nos visiteurs en herbe, il est possible d’assister ici à toutes les étapes de fabrication d’un jean, depuis sa découpe à son assemblage, jusqu’à l’étape finale du lavage de finition. La réussite de notre laboratoire, la plus remarquée à ce jour, est une technologie appelée « Blue Cycle » : cette technique de fabrication permet de réduire de 99 % la quantité d’eau nécessaire au délavage des jeans (en comparaison entre notre modèle de jean coupe droite pour homme sorti en 2017 et le modèle actualisé sorti en 2018, les volumes d’utilisation en eau pouvant varier selon le produit). Récemment, nous avons reçu la visite d’un groupe d’écoliers du quartier, eux-mêmes habillés en denim. Ces quatre amis ont été stupéfaits à la vue de ces imposantes machines à laver installées au beau milieu du laboratoire. Il faut reconnaître qu’une seule de ces machines est aussi énorme que notre groupe d’écoliers à lui tout seul. Pour débuter leur visite en immersion, nous les avons confiés aux bons soins de Thomas, chargé de la découpe des patrons dans la salle de couture. « C’est le morceau de tissu qui se transforme en poche ? », lui demande Issa, manifestement débordante de curiosité. Après être tombés d’admiration devant les différents motifs de tissu et après avoir passé en revue les échantillons de denim qui tapissent les murs du laboratoire, nos écoliers en herbe se sont ensuite dirigés vers la zone technique dénommée Blue Cycle Area.
Découper et coudre
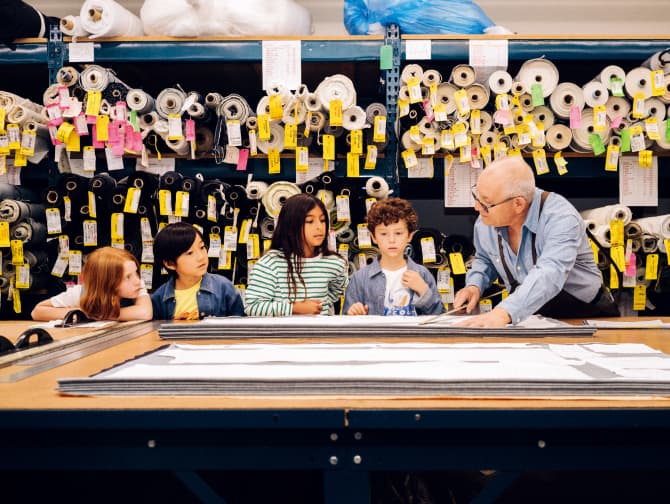
La toile de jean amidonnée est empilée sur une épaisseur de dix couches de tissu. Elle est ensuite démarquée au patron, puis découpée à l’aide d’une machine spécialisée qui fonctionne comme une scie alternative. « Ça, c’est la poche ! » s’exclame Surya dans sa chemise rayée.
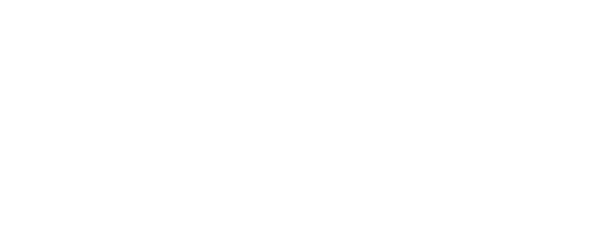
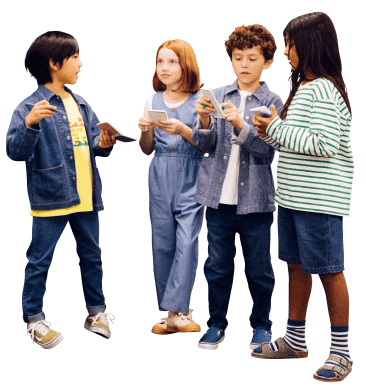
Ce qui rend cette technologie totalement inédite, c’est qu’elle reproduit fidèlement l’effet du laser. D’un pas prudent, le groupe s’approche d’une de ces énormes machines, chargée d’une paire de jean rigide, tout droit sorti de l’atelier d’assemblage. Puis soudain, une bouffée de fumée apparaît... suivie d’une flamme et d’un bourdonnement très bref, comme une décharge électrique, qui fait sursauter Surya. Elle se bouche les oreilles et trépigne d’émerveillement. En quelques secondes, le jean ressort tout usé et élimé. Elan s’aventure le premier à toucher la zone déchirée. « C’est un rayon laser qui a fait ça ? », demande-t-il. « C’est exactement ça ! », lui répond Juan, notre technicien. « Le laser brûle le tissu selon un modèle créé sur ordinateur. Nous avons installé des machines comme celle-ci dans toutes nos usines, notamment au Bangladesh ». Autrefois, les jeans étaient traités à la main en atelier, avec du papier de verre. Mais l’expérience a montré que ce procédé conduisait à des résultats variables. Il présentait surtout des risques pour la santé du personnel, en raison de la poussière dégagée par le tissu élimé. Depuis que ce nouveau procédé au laser a été introduit, nos usines sont en capacité de produire en masse des quantités de jeans de qualité identique et sans danger pour la santé.
Pour la prochaine étape du processus de fabrication, nos visiteurs en herbe sont allés voir de plus près ces énormes machines à laver. Darwin, notre responsable technique, ouvre la porte du tambour. C’est alors que s’échappe une vapeur épaisse. Et pourtant, il n’y a presque pas d’eau à l’intérieur de la machine. « Elle sert à quoi, cette vapeur ? », demande Sylvie. Le lavage du jean comporte un certain nombre d’étapes. Tout d’abord, l’amidon est libéré du tissu en transformant ce que nous appelons le « denim brut » en tissu lavé. Ensuite, le jean est lavé à plusieurs reprises pour lui donner un aspect authentiquement délavé avec des effets d’usure appelés « atari ». Ce procédé nécessite habituellement d’énormes quantités d’eau. Ce qui a révolutionné ce processus, c’est une technique de lavage à la vapeur qu’on appelle « lavage aux nanobulles ». Au lieu d’être plongé dans l’eau durant l’étape de lavage, le jean est aspergé de petites quantités de vapeur à haute pression. Pour lui apporter une touche finale, le tissu est ensuite patiné à l’issue d’une ultime étape, qui est le « lavage à l’ozone ». Il s’agit d’utiliser du gaz d’ozone pour oxyder la teinture contenue dans le denim, afin d’obtenir un effet nettement blanchi et naturel.
Ce procédé utilise quand même de l’eau, mais en quantité infime. Dans le même état d’esprit, notre laboratoire a également développé un système adapté pour le recyclage de l’eau. Grâce ce nouveau processus, on utilise la puissance de l’ozone et d’autres minéraux pour éliminer les colorants et les produits chimiques contenus dans l’eau résiduelle bleue qui sort du lavage. Cette eau est ensuite filtrée pour retrouver sa clarté.
Ces techniques de nouvelle génération nous permettent de créer des jeans authentiquement délavés, pour la plus grande satisfaction de nos clients qui les portent. Nous espérons que nos quatre visiteurs en herbe se rappelleront leur périple en immersion dans nos ateliers, lorsqu’ils revêtiront à leur tour nos jeans LifeWear. C’est cette espérance et notre foi dans nos techniques de fabrication qui nous incitent à poursuivre nos recherches dans ce laboratoire.
Traitement au laser
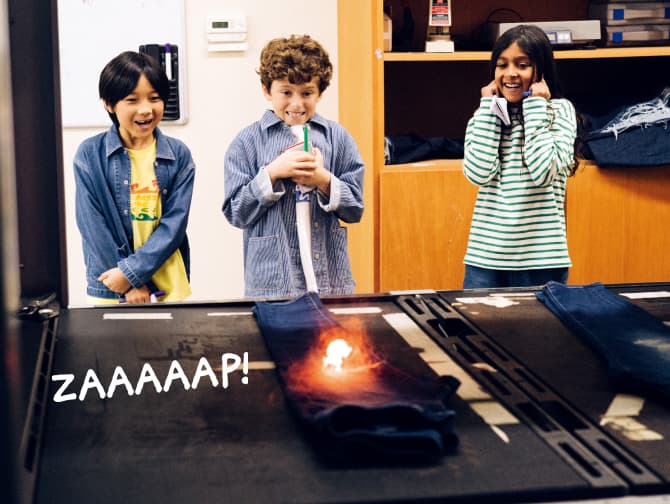
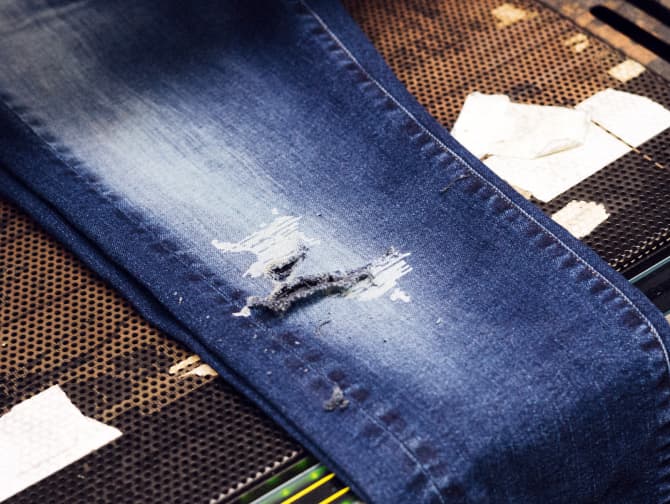
Les processus extrêmes comme le vieillissement au laser dégagent des flammes et des étincelles. Il s’agit d’un procédé propre sur le plan environnemental, car les chutes de tissu sont incinérées sur place, tandis que les émanations de fumées est aspirée par le bas.
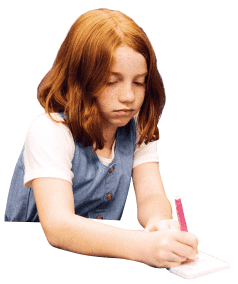
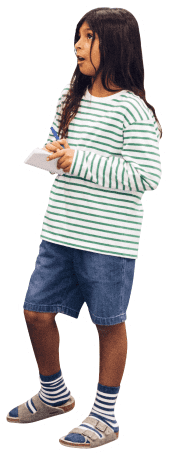
Pour la prochaine étape du processus de fabrication, nos visiteurs en herbe sont allés voir de plus près ces énormes machines à laver. Darwin, notre responsable technique, ouvre la porte du tambour. C’est alors que s’échappe une vapeur épaisse. Et pourtant, il n’y a presque pas d’eau à l’intérieur de la machine. « Elle sert à quoi, cette vapeur ? », demande Sylvie. Le lavage du jean comporte un certain nombre d’étapes. Tout d’abord, l’amidon est libéré du tissu en transformant ce que nous appelons le « denim brut » en tissu lavé. Ensuite, le jean est lavé à plusieurs reprises pour lui donner un aspect authentiquement délavé avec des effets d’usure appelés « atari ». Ce procédé nécessite habituellement d’énormes quantités d’eau. Ce qui a révolutionné ce processus, c’est une technique de lavage à la vapeur qu’on appelle « lavage aux nanobulles ». Au lieu d’être plongé dans l’eau durant l’étape de lavage, le jean est aspergé de petites quantités de vapeur à haute pression. Pour lui apporter une touche finale, le tissu est ensuite patiné à l’issue d’une ultime étape, qui est le « lavage à l’ozone ». Il s’agit d’utiliser du gaz d’ozone pour oxyder la teinture contenue dans le denim, afin d’obtenir un effet nettement blanchi et naturel.
Lavage aux nanobulles
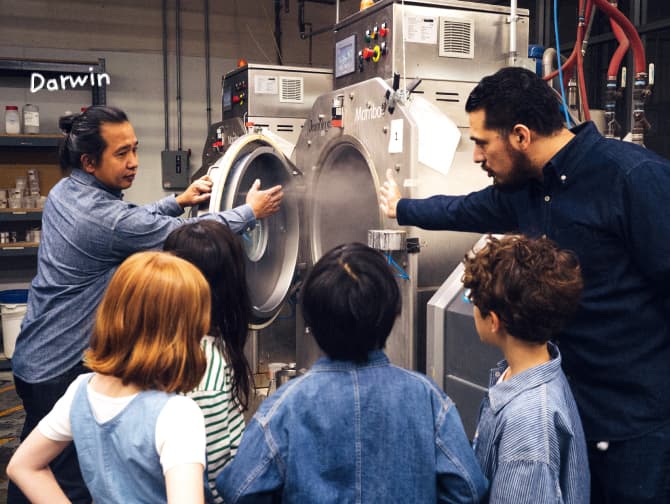
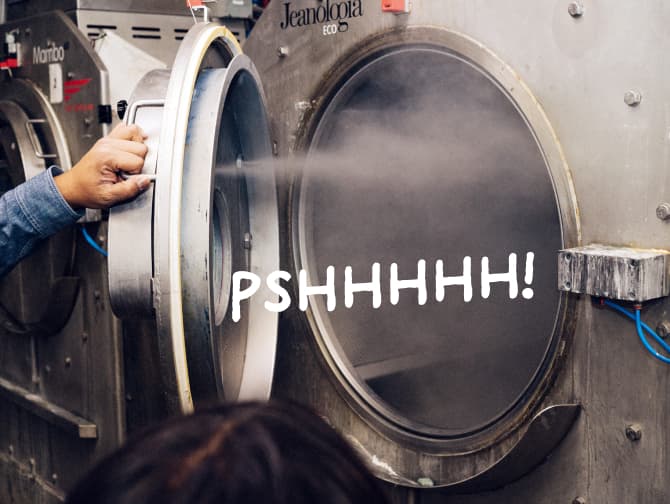
Vous voyez cette vapeur qui s’échappe du hublot de la machine ? Éjectée à haute pression dans le tambour, elle permet d’extraire la couleur du jean.
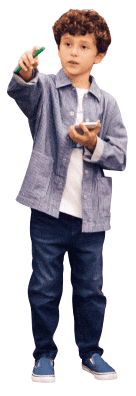
Lavage à l’ozone
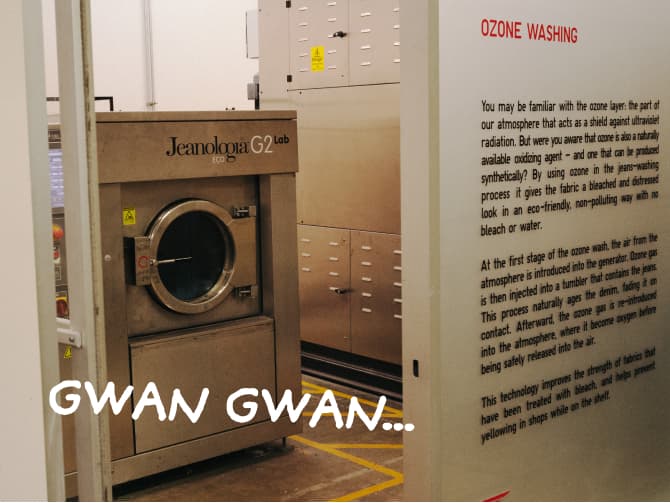
L’ozone est utilisé pour blanchir les jeans dans ce lave-linge à tambour.
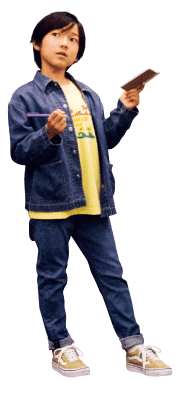
Ce procédé utilise quand même de l’eau, mais en quantité infime. Dans le même état d’esprit, notre laboratoire a également développé un système adapté pour le recyclage de l’eau. Grâce ce nouveau processus, on utilise la puissance de l’ozone et d’autres minéraux pour éliminer les colorants et les produits chimiques contenus dans l’eau résiduelle bleue qui sort du lavage. Cette eau est ensuite filtrée pour retrouver sa clarté.
Ces techniques de nouvelle génération nous permettent de créer des jeans authentiquement délavés, pour la plus grande satisfaction de nos clients qui les portent. Nous espérons que nos quatre visiteurs en herbe se rappelleront leur périple en immersion dans nos ateliers, lorsqu’ils revêtiront à leur tour nos jeans LifeWear. C’est cette espérance et notre foi dans nos techniques de fabrication qui nous incitent à poursuivre nos recherches dans ce laboratoire.
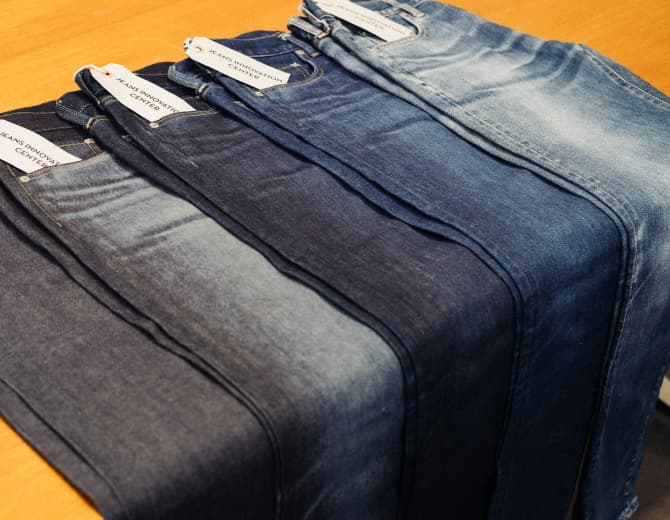
Des échantillons de jeans illustrent ici chaque étape de leur fabrication. De gauche à droite : un denim brut, un denim après traitement au laser, un denim après différentes étapes de lavage aux nanobulles, et enfin un denim après traitement à l’ozone.
- Elan
-
- Veste en denim enfant 49,90 $
- T-shirt graphique en coton AIRism enfant 19,90 $
- Jean fuselé extra extensible enfant 34,90 $
- Issa
-
- Veste en denim enfant 49,90 $
- T-shirt graphique en coton AIRism enfant 19,90 $
- Jean doux extra extensible enfant 39,90 $
- Sylvie
-
- Combinaison-pantalon fille (Ce produit n'est pas disponible au Canada.)
- T-shirt en coton enfant (Ce produit n'est pas disponible au Canada.)
- Surya
-
- T-shirt rayé col rond enfant (Ce produit n'est pas disponible au Canada.)
- Short à enfiler en denim extensible 24,90 $
- Chaussettes 14,90 $
- Photographie : Kohei Kawashima
- Stylisme : Mitsuru Kurosawa
- Coiffure et maquillage : Anna Kato
- Coordination : Megumi Yamano
- Remerciements particuliers à Naoyasu Mera et Aya Mutoh
- English
- Français