JEANS
INNOVATION
It’s all about the future.
UNIQLO is challenging the status quo
for making jeans.
At the JEANS INNOVATION CENTER in Los Angeles, California, UNIQLO is rethinking the way that jeans are made by updating the methods and materials of jean production with an eye toward the future.
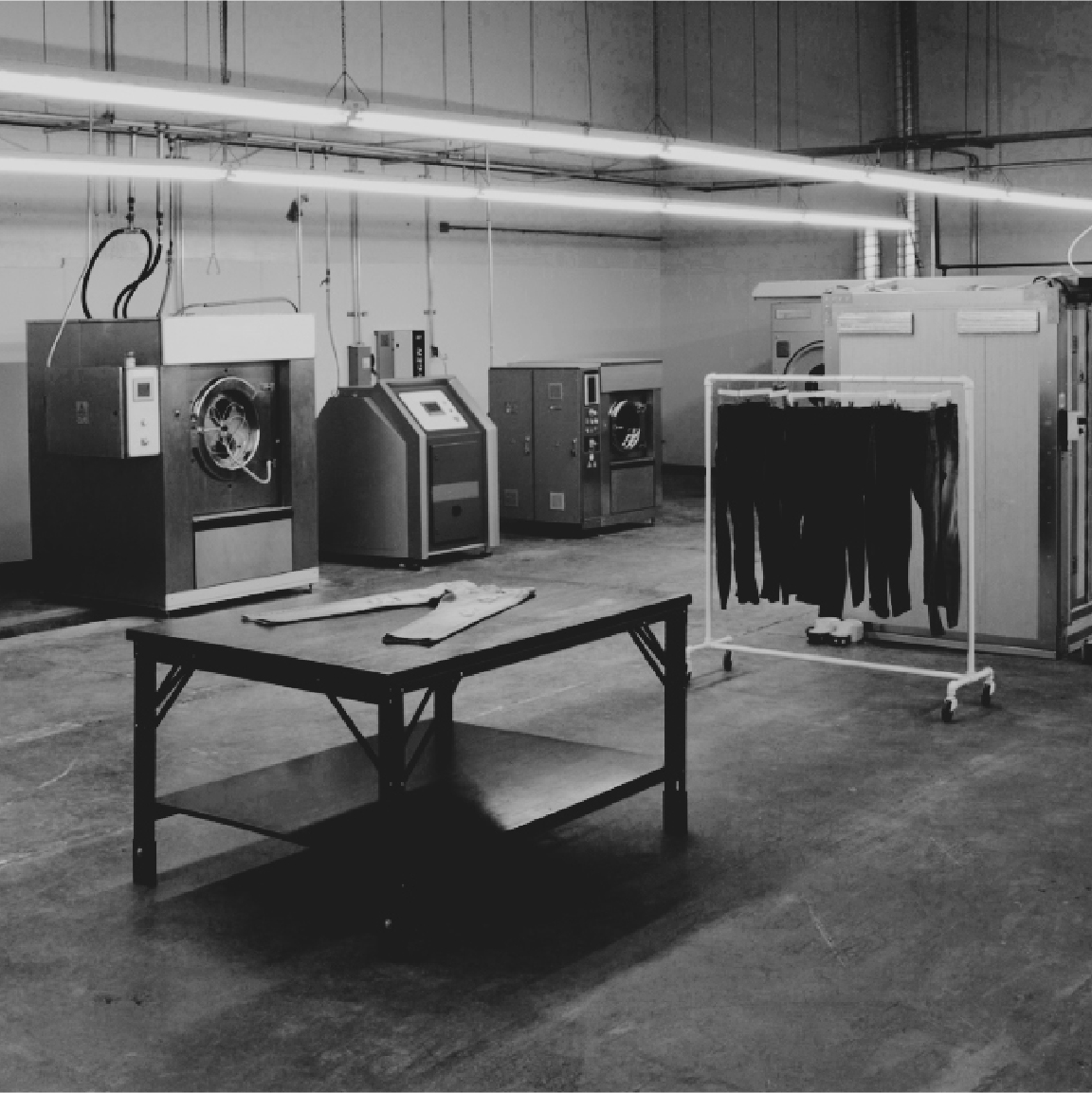
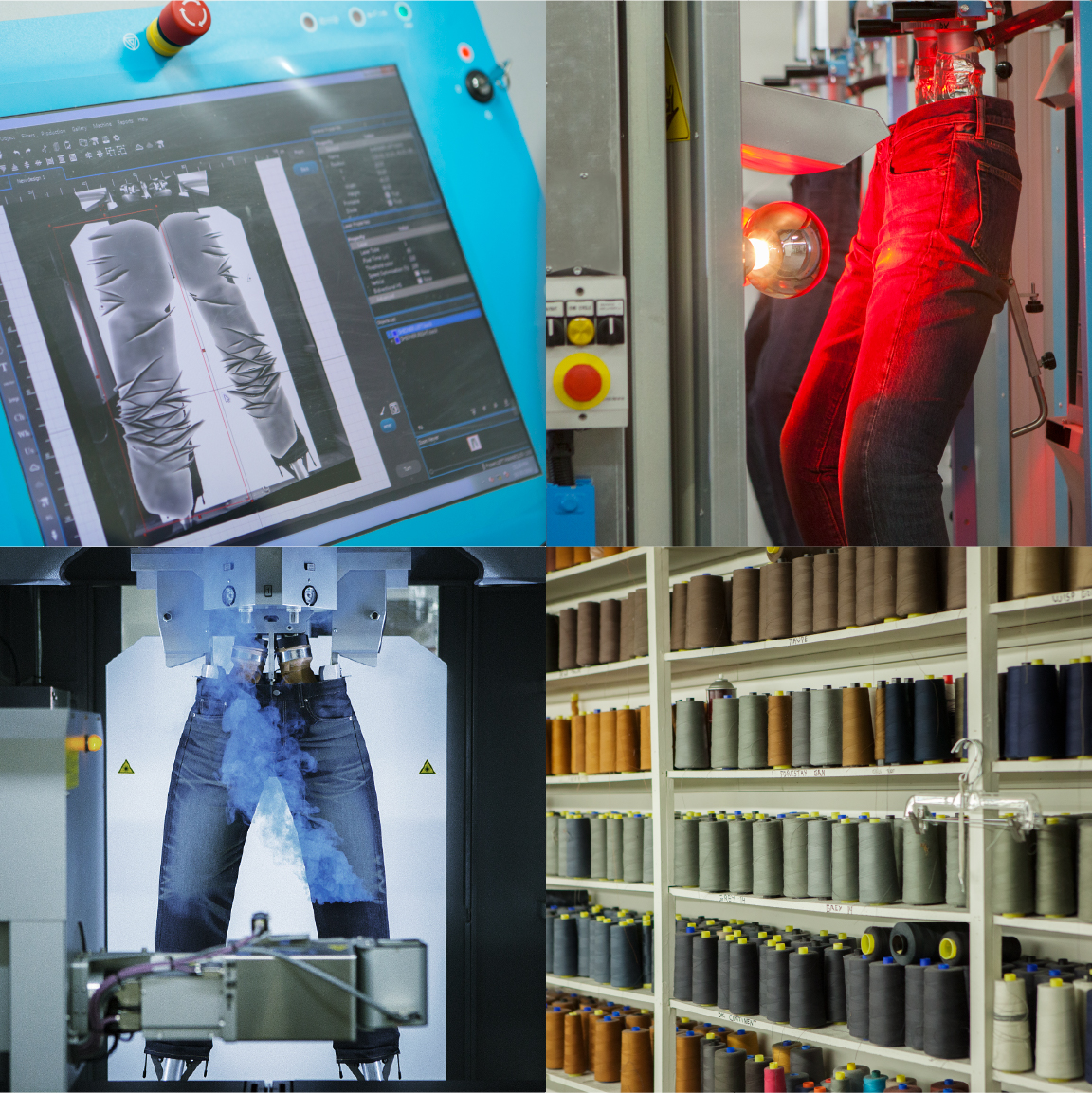
“BLUE CYCLE” Technological Developments
in Final Finishing Process
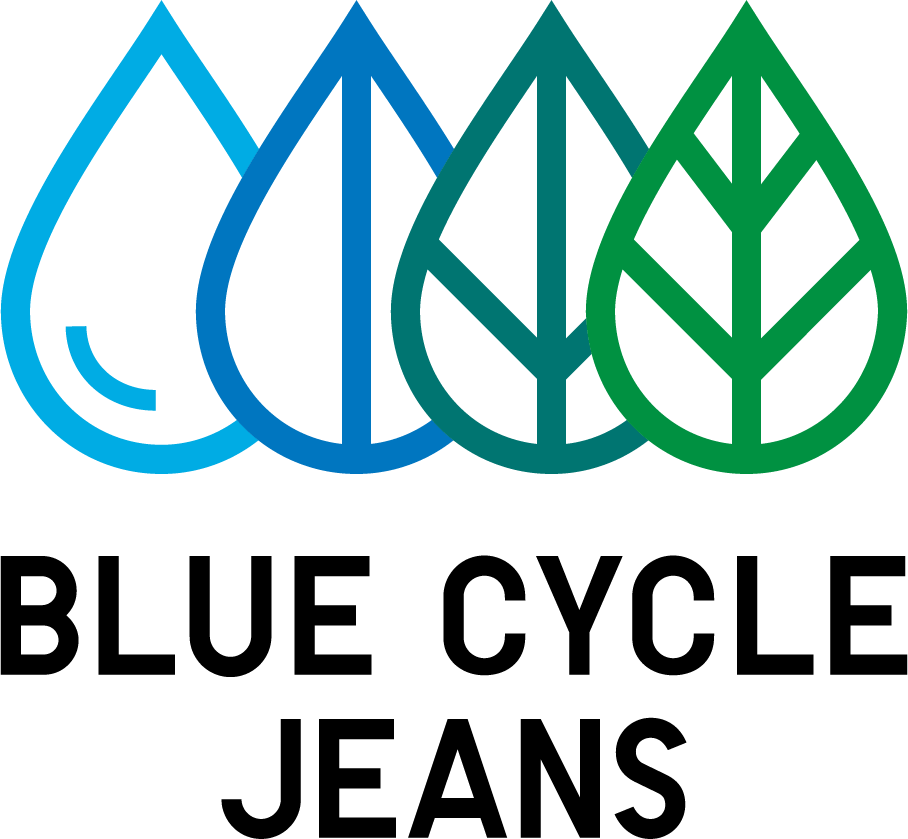
Aimed to reduce the burden on personnel and the amount of water required, BLUE CYCLE is a finishing technology introduced by the JEANS INNOVATION CENTER in Los Angeles in 2018. Traditional final finishing processes for making dameged jeans appear to have aged naturally require large amounts of manual labor and water. The burden posed on the environment and workers is considerable. Working toward a solution, the JEANS INNOVATION CENTER has incorporated laser distressing techniques and revamped the machines and detergents used in the washing steps. In 2018, the first pairs of men’s regular fit jeans were made using BLUE CYCLE technology. By 2020, this technology was being used for a variety of jeans made and sold by UNIQLO*.
*Technique not used for jeans lacking distressed features.
Switching from Manual Labor to Lasers
Traditional techniques for distressing jeans involved abrading denim by hand using sandpaper or applying chemicals directly to the fabric to achieve a creased, vintage look. Such work required the use of caustic chemicals as well as the laborious process of treating each garment by hand. By using laser technologies to create distressed effects through digital means, the JEANS INNOVATION CENTER has updated these processes so that manual labor is no longer needed.
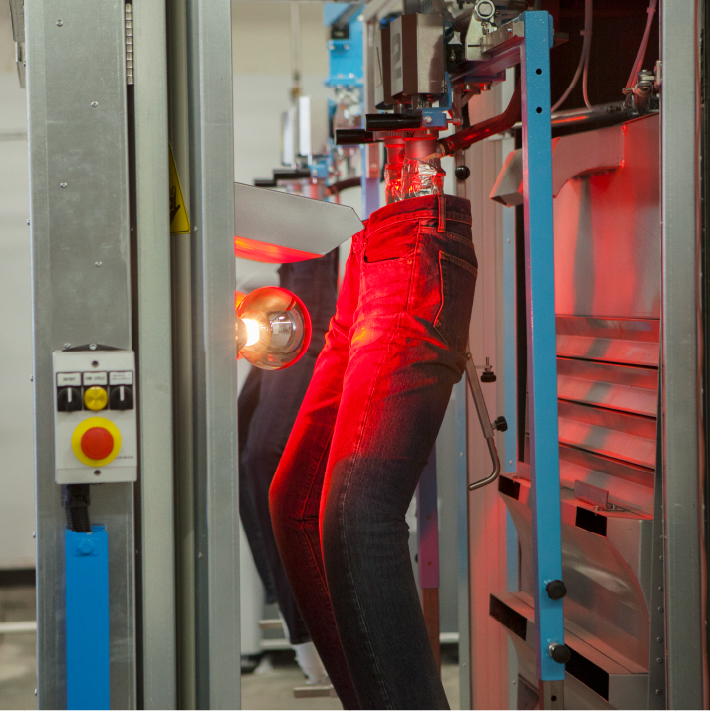
Developing a Recipe for Low-Water
Finishing Techniques
In traditional washing processes for giving denim a faded look, jeans are laundered using stone and large quantities of water, physically damaging the material so as to create the intended effect. To update this technique, the JEANS INNOVATION CENTER developed a proprietary recipe using detergents, ecostones, nano bubble technology, and ozone gas. By reinventing these techniques, the amount of water needed for these finishing effects has been notably reduced*.
*Up to 99%. Data is based on a comparison between Men‘s Regular Fit Jeans (68 BLUE) 2017 and 2018 using technology developed in 2018 by our Jeans Innovation Center. Water savings may vary slightly between products.
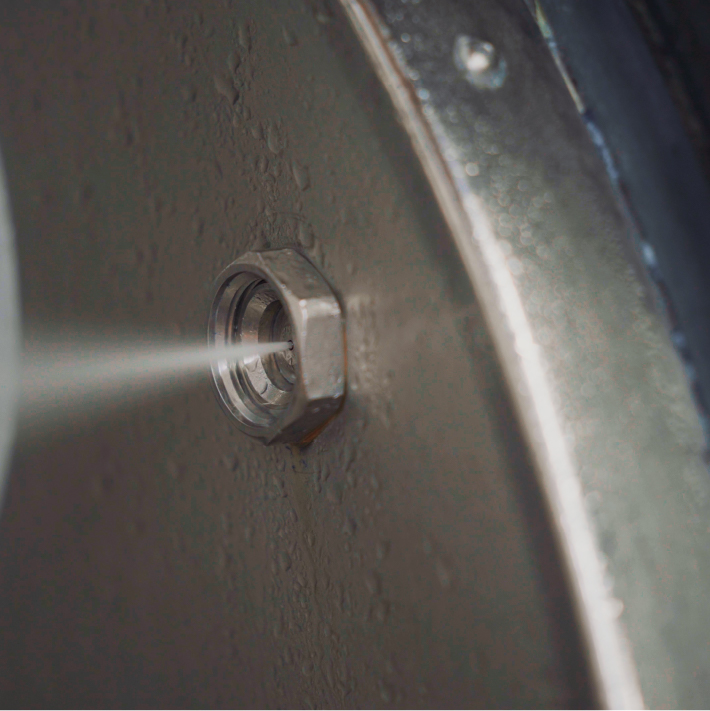
UPDATED / 2025.02.28
Most Viewed Contents
-
PEACE FOR ALL
A SINGLE T-SHIRT HAS THE POWER TO SPREAD PEACE. “It’s time for action, in the name of world peace.” Major figures who share this vision with...
Read More
-
RE.UNIQLO STUDIO
Your UNIQLO clothes have a long life ahead of them. We're creating something positive for the future by keeping UNIQLO items in circulation....
Read More
-
UNIQLO DOWN RECYCLE
Recycling clothes into clothes, UNIQLO’s latest challenge that opens up new links between people, clothing, and the global environment. We are...
Read More
-
UNIQLO PRE-OWNED CLOTHES PROJECT by RE.UNIQLO
Once you’ve made the most of your clothes, it’s time to recycle. RE.UNIQLO is working towards a circular society by selling pre-owned clothes.....
Read More
Recommended Contents
-
RE.UNIQLO
Can your old clothing improve the future? Yes! At UNIQLO, we recycle your used garments through our circular sustainability programs. Take our recycled down ini...
Read More
-
JEANS INNOVATION
At the JEANS INNOVATION CENTER in Los Angeles, California, UNIQLO is rethinking the way that jeans are made by updating the methods...
Read More
-
GENDER
All women should be able to pursue their dreams and forge a new tomorrow. We want to see women enjoy infinite possibilities. Believe in a world that enables wom...
Read More
-
PREPARING CLOTHES FOR AN EMERGENCY DISASTER
UNIQLO has aided disaster victims around the world over the past 20 years. It has learned in the process that few people prepare clothing kits for such emergencies...
Read More
Newest Contents
-
UNIQLO PRE-OWNED CLOTHES PROJECT
Once you’ve made the most of your clothes, it’s time to recycle. RE.UNIQLO is working towards a circular society by selling pre-owned clothes.....
Read More
-
SPECIAL OLYMPICS
Special Olympics is an international organization that provides sports training and competition for people with intellectual disabilities...
Read More
-
JEANS INNOVATION
At the JEANS INNOVATION CENTER in Los Angeles, California, UNIQLO is rethinking the way that jeans are made by updating the methods...
Read More
-
THE SETOUCHI OLIVE FOUNDATION
The Setouchi Olive Foundation is a not-for-profit organization established by world-renowned architect Tadao Ando and Kohei Nakabo....
Read More