Improving supply chain transparency and establishing traceability
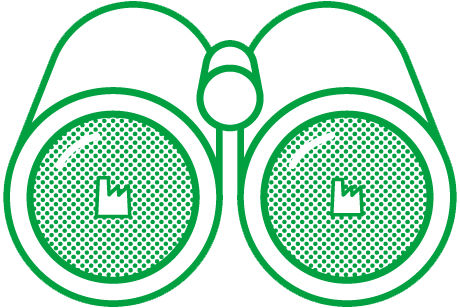
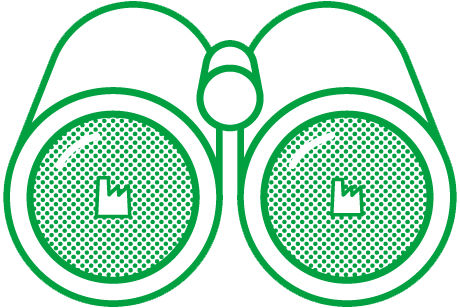
Fast Retailing believes that respecting fundamental human rights and ensuring the health, safety, and security of all workers in our supply chain is our most important responsibility. We have a zero-tolerance policy regarding human rights violations (especially child labor, forced labor, harassment, discrimination, and violence), and work with our production partners to build systems and ensure compliance.
Key Initiatives and Progress
Disclosing information that gives customers peace of mind
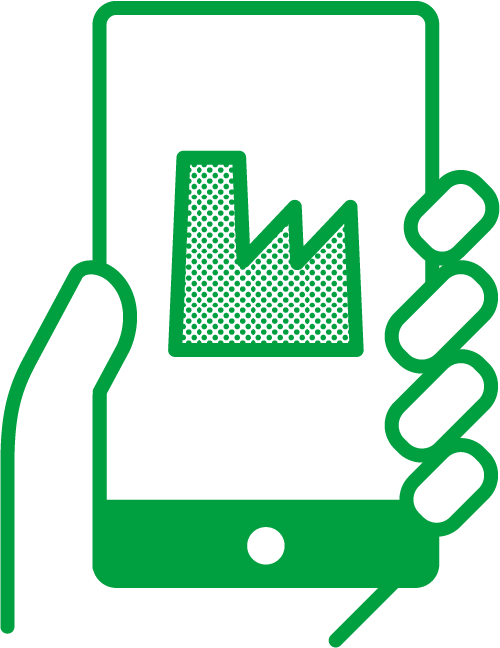
Disclosing information that gives customers peace of mind
We aim to improve transparency as we establish greater traceability
We want our customers to be able pick up our products with trust and use them for a long time, so we have started to provide information on where and how each individual product was made. From August 2023, UNIQLO and GU online stores in some countries created a new item on individual product pages, entitled “Impact on the planet and society.” Currently, this column displays information on where each product was produced. Going forward, we plan to expand this initiative to other markets, and explore exactly what information our customers really need so we can expand the amount of information offered.
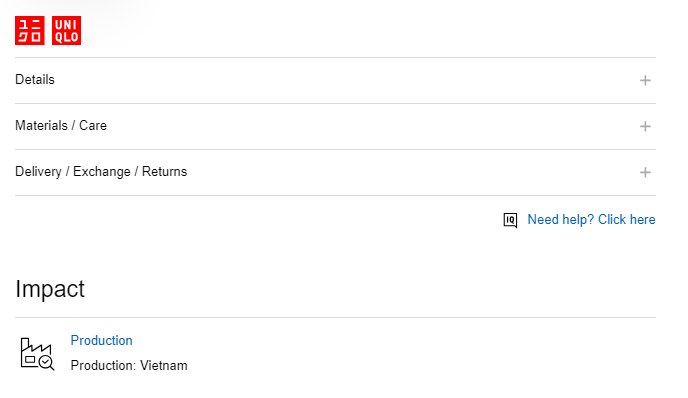
Workplace monitoring and evaluation
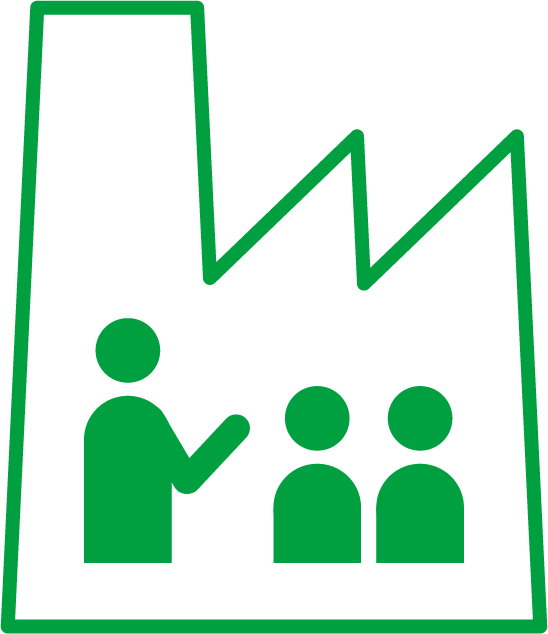
Implement more effective monitoring to improve working environments
Fast Retailing requires its partner factories comply with the Code of Conduct for Production Partners set up in 2004 and monitors working environments based on this code. Employees from the Production Department, which is responsible for product quality and production process management, are assigned to our production offices in Shanghai, Ho Chi Minh City, Dhaka, Jakarta, and Bangalore and visit supplier factories on a weekly basis. There, they can gain a clear understanding of how the factories operate, offer guidance on correct production process, and promote responsible procurement hand in hand with our production partners. We also publish lists of all our garment factories and core fabric mills, and factories to which some parts of the production process are outsourced.
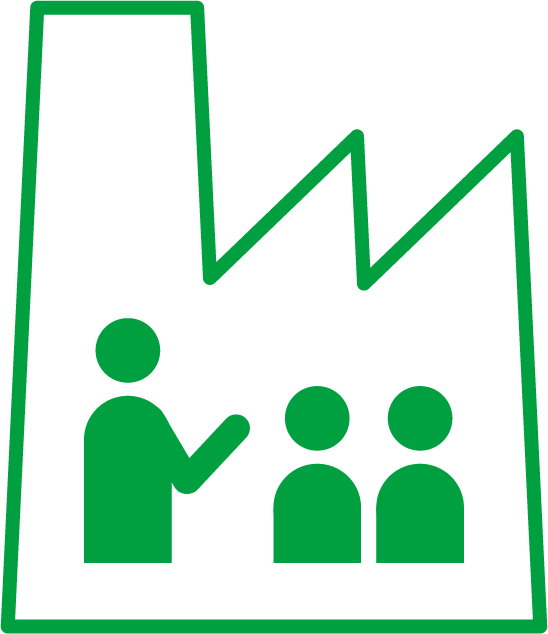
Empowerment program for women in Bangladesh
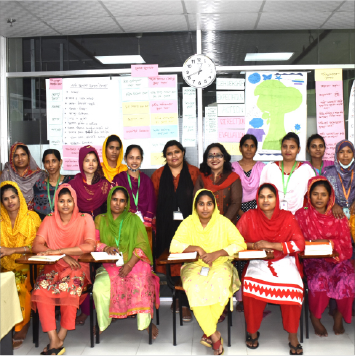
Empowerment program for women in Bangladesh
Career-building support for aspiring female managers
In March 2023, we added targets to our Women’s Empowerment Program in Bangladesh as part of our ongoing efforts to help women working in the garment industry advance their careers. More specifically, we set targets to ensure (1) 1,500 female employees receive management training, (2) the ratio of female managers at target factories is increased to an average of 30% or higher, and (3) all female employees can get easy access to daycare centers and services, services that promote better physical and mental health, and a safe means for commuting to work. We aim to achieve these targets by the end of 2025 with the help of eight of our core garment factories in Bangladesh. To date, we have offered leadership and technical skills training for aspiring female managers. At the end of fiscal 2022, 163 women, or 51% of the women who took part in the training, had been promoted to management positions. The program has expanded training opportunities and encouraged more women to go out into the workforce, but now it is focusing on building environments in which women can play an active role and feel comfortable in their job.
Most Viewed Contents
-
PEACE FOR ALL
A SINGLE T-SHIRT HAS THE POWER TO SPREAD PEACE. “It’s time for action, in the name of world peace.” Major figures who share this vision with...
Read More
-
RE.UNIQLO STUDIO
Your UNIQLO clothes have a long life ahead of them. We're creating something positive for the future by keeping UNIQLO items in circulation....
Read More
-
UNIQLO DOWN RECYCLE
Recycling clothes into clothes, UNIQLO’s latest challenge that opens up new links between people, clothing, and the global environment. We are...
Read More
-
UNIQLO PRE-OWNED CLOTHES PROJECT by RE.UNIQLO
Once you’ve made the most of your clothes, it’s time to recycle. RE.UNIQLO is working towards a circular society by selling pre-owned clothes.....
Read More
Recommended Contents
-
RE.UNIQLO
Can your old clothing improve the future? Yes! At UNIQLO, we recycle your used garments through our circular sustainability programs. Take our recycled down ini...
Read More
-
BLUE CYCLE JEANS
At UNIQLO, we are creating jeans that respect the future of our planet. Jeans born from cutting-edge technology,developed in our Los Angeles-based Jeans innovat...
Read More
-
GENDER
All women should be able to pursue their dreams and forge a new tomorrow. We want to see women enjoy infinite possibilities. Believe in a world that enables wom...
Read More
-
PREPARING CLOTHES FOR AN EMERGENCY DISASTER
UNIQLO has aided disaster victims around the world over the past 20 years. It has learned in the process that few people prepare clothing kits for such emergencies...
Read More
Newest Contents
-
PEACE FOR ALL
A SINGLE T-SHIRT HAS THE POWER TO SPREAD PEACE. “It’s time for action, in the name of world peace.” Major figures who share this vision with...
Read More
-
CLOTHING MADE FROM RECYCLED MATERIAL
Our ability to recycle materials is growing as recycling technology evolves. New...
Read More
-
RE.UNIQLO STUDIO
Your UNIQLO clothes have a long life ahead of them. We're creating something positive for the future by keeping UNIQLO items in circulation....
Read More
-
COMMITMENT TO REDUCING SINGLE-USE PLASTIC
Around 8 million metric tons of plastic debris enters the oceans every year. Around 80% of that debris comes from towns and cities, so it is important....
Read More